
Grippers
​
-
Grippers are the main effectors used to hold pieces or objects.
-
Grippers are devices that can be used to hold or hold objects.
-
You can place mechanical handles and hooks, magnets and suction devices that can be used to hold and hold them inside.
-
The gripper take advantage of point-to-point controls (robots have a full path between those who love themselves and where they are placed).
-
The grippers should be designed in such a way that they need a minimum amount to handle part of the job.
-
Application of holders: - Heavy equipment, conveyor, material handling, bottle transport, pallet parts etc.
THE GRASPING PROCESS
The complexity of the grasping process is usually less because it is very familiar to humans. However, there are several problems with automating this process. Gripper design not only depends on the requirements of the partnership, but the steps such as handling, movement, and release are affected by the previous steps, such as step and step. In simple words, the defective pieces require less versatile claws, while high acceleration, re-fixation and high precision are required
The grasping process (Figure 1) can be divided into the following steps:
Approaching the object: This step is the one during which the gripper is positioned close to the object.
Coming into Contact: The Gripper contact with the work-piece is received up to this point. In cases of non-contact operation, the work-piece is in the force range of the gripper.
Increase Strength: This strength increase must be within certain limits so that the prehended parts neither get damaged nor left outside the jaw.
Protecting the object: When enough force is applied, the object's full degree of freedom is removed and the object stops moving independently of the Gripper.
Moving the object: this stage involves moving the object to the desired location.
Drop the object: In the macro scale, the object is usually released by gravity.
To determine the effectiveness of the grasping, it is necessary to monitor each step, which can be done using various sensors like force sensors, torque sensors, slip sensors, contact sensors etc.
THE RELEASING PROCESS
When the grasping principle is inactivated, the object is usually released by gravity. However, in some cases, gravity alone is not enough because the pressure of grasping force retention continues after it becomes inactive. In the case of magnetic grippers or micro-scale adhesive grippers, only gravity is not sufficient. It tells you the strategies of active and passive launch to allow a reliable and passive release.
Resolutions have shown that the resolution can be divided into two groups: passive Strategies: Reducing surface forces and active strategies: Where additional forces allow the object to be released.
Types of Grippers
-
Mechanical Grippers
-
Hooks and Scoops
-
Magnetics Grippers
-
Vacuum Grippers
-
Expandable Bladder Type Grippers
-
Adhesive Grippers
< Mechanical Grippers
-
We can think of a mechanical grinder as a robotic arm. The original robot will have only two or three fingers in hand
-
A mechanical hand that contains matter depends on the friction to protect the retention of the object.
-
Friction between the clamp and object is based on two things: the first is the type of surface which is metal in metal, the rubber in the metal, the smooth or rough surface, and the other force which suppresses the surface.
-
Generally, mechanical grippers are equipped with certain types of pads, which are usually made of polyurethane because they provide more friction. Cushions that damage the work area are less. A cushion is also used to maintain a good adhesion because polyurethane will come in contact with all parts of the surface when the handle will be closed.
-
Mechanical Gripper can be designed and manufactured for specific purposes and can be arranged according to the size of the object. They can also have double claws. We all say that 'two arms are better than one' and robots gain profit in double paws because they can increase productivity, machines can be used with two machines where one robot in one operation has two parts Can take it. In this, the operation of machines changes the size of the object or part and where the time of the cycle of the robot with the production of other machines is slow.
In a mechanical gripper, the holding of an object can be done by two different methods such as:
1) Using the finger pads as like the shape of the work part.
2) Using soft material finger pads.
In the first method, the contact surface of the fingers has been designed based on the workpiece to achieve the estimated size. It will help fingers to choose the part of a workpiece to a specific degree.
In another method, fingers should be able to provide enough power for the job. To avoid scratches on a piece of work, fingers have soft skills. As a result, co-secretion of the finger contact surface and an increase in friction. This method is very simple and less expensive. If the applied force against the workplace is in a parallel direction, it can cause a slip. Sleeping can be avoided by presenting subtle things based on forced force.
µ nfFg= w ………………… 1
µ => coefficient of friction between the work part and fingers
nf=> no. of fingers contacting
Fg=> Force of the gripper
w => weight of the grasped object
If we are more than weights for working cut, we should change equation 1.
µ nfFg= w g …..……………. 2
g => g factor
During fast grip operation, the work portion will be doubled. To get rid of this, improved equation 1 has been presented by Anglo Berger. The factor g in equation 2 is used to compute acceleration and gravity.
The values of g factor for several operations are given below:
-
g = 1 – acceleration supplied in the opposite direction.
-
g = 2 – acceleration supplied in the horizontal direction.
-
g = 3 – acceleration and gravity supplied in the same direction.
Where they use in industry
This type of grippers are commonly used in high volume case transporting operations and features:
-
High case throughput
-
Significant operating space
-
Higher initial cost, maintenance cost
< Hooks and Scoops
-
Hooks and scoops are the easiest types of end effects that can be classified as grippers.
-
Scoop or shell is usually used to cover the molten metal and move it into the mould.
-
Especially if no specific condition is required and if it is only immersed in the liquid, then it may be a hook to participate.
-
The hook is used to load and discharge components of the suspension. Parts made by hooks have a strap, eye or ring to activate it.
-
Scoop is used to manipulate liquid or energy content, the extent of excavation is that it is difficult to control the amount of martial force in this radius. In addition, there is a need to monitor the spread of the material.
Where they use in industry
Can use anywhere because it’s simple gripper (as simple pick-and-place assembly)
<Magnetic Grippers
-
Magnetic grippers work exclusively on magnetic objects and are therefore limited to working with some metals.
-
For maximum effect, the magnet must be open on the metal surface. Any air space reduces the power of magnetic force, so metal plates are more suitable for magnetic handles.
-
If the magnet is strong enough, magnetic resources can freely lift the object. In some cases, the size of the magnet resembles the size of the object
-
There is a loss of use of magnetic paws. Permanent magnets break into the heat and hence there is a fear that the longer contact with the hectic work piece will make them weak at that point where they can no longer be used. The effect of heat will be based on the moment it comes in contact with the hot part. Most magnetic substances are relatively ineffective by temperatures up to 100 degrees.
-
The electromagnet can be used instead, and DC is powered by an electric current and when the power is closed, it loses almost all magnetism.
-
Explosive atmosphere occurs and spark resistant magnet is also used from electrical appliances
Where they use in industry
Magnetic grippers are used in a variety of industries where products or components contain ferrous metal. Latest applications of magnet grippers include material handling, palletizing, and bin picking of automobile parts and palletizing metal containers like paint and solvent cans and other steel containers.
< Suction Grippers
Suction grippers are of two types:
1. Vacuum-Driven Device - Vacuum may be provided by vacuum Pump or by Compressed Air
2. Flexible suction cup containing device - press the cup on the work piece. To free the work piece, the compressed air is thrown into the suction cup. The advantage of the suction cup is that if there is a failure of electricity, it will work because there is no shortage of work. The problem of suction cup is that it works only on a clean, smooth surface.
There are many more advantages to using suction cups instead of mechanical grip: There is no risk of crushing delicate things, exact shape and size do not matter, and suction cups are not necessarily locally located on the object.
At the end of the suction cup, the following are effective: Robot system should have a type of pump for air and in some cases the noise level can be upset.
Where they use in industry
Vacuum grippers are commonly used for material handling of flat, smooth objects (like building materials – foam insulation and boards) or corrugated cases in palletizing applications. Another common use, especially in the food and beverage industry, is case packing pouches. Pouches, or soft flexible packaging, are becoming very popular because of the reduction in packaging waste associated with their use.
< Expandable Bladder Type Grippers
-
Bladder grip or bladder arm is particularly effective robotic end, which can be used to capture, catch and move rod shapes or cylindrical objects.
-
The main element of the grip is a powerful, donut-shaped or cylindrical sleeve that usually resembles the cuff used in blood pressure measurement equipment.
-
A sleeve is kept so that the material is captured and then spread to the sleeve, until the desired work is completed.
-
Effective pressure measurement force by the sleeve can be measured and regulated by using force sensor.
-
Bladder gripper is useful in managing delicate items. However, they do not work fast, and can only work with objects within a narrow range of physical size.
< Adhesive Grippers
Adhesive material can be used for action on adhesive grippers.
In adhesive grippers, adhesive material reduces its losses due to repeated use. This reduces the reliability of the grinder. To overcome this problem, the gripper is fed continuously as a tape, feeding the adhesive material.
The main property of adhesive grippers is the fact that until adhesive retains its viscosity, it is easy, however, there are some limitations, the most important fact is that adhesive cannot be easily removed. Some other media, such as tools that lock the object, should be used.
Adhesive handles were used to handle fabrics and other lighter material.
Where they use in industry
Gripper designs in which an adhesive substance perforce the grasping action can be used to handle fabrics and other lightweight materials. The requirements on the items to be handled are that they must be gripped on one side only. Deploying adhesive substances these hold flexible materials, such as fabric.
Examples
Example 1. Design and fabrication of soft gripper using 3D printer
Soft robotics is a specific field of robotics technology dedicated to the creation of highly compatible content found in living organisms.
The soft robotics technique is based on how the live organisms move mainly and the environment accepts it. Unlike robots made with heavy materials, soft robots offer more flexibility and adaptability to work, as well as providing more security when working with people.
The first example of a soft robot clamp with a seam model's modular design, which can accommodate many types of things. The soft gripper consists of four commonly-connected fingers and a bracket used to connect the clip to the robot. All the ingredients were printed in 3D and soft fingertips are made with platinum treated silicone rubber through molding technology. Fingers are analyzed by the use of limited element analysis (FI) by applying different loads. The finger Flexi is obtained by providing pressure air. A curved sensor is integrated into each finger to measure the angle of turn or curvature during the grip. The proposed clamp can grip and lift objects with different shapes and weight.
Soft Grip Robot is also used primarily for selection and placement experiments and other functions. Example: Your fish robot clamp may contain soft materials like eggs, fruits, paper nuts, etc. This process of soft grippers requires some processes, such as modeling, analysis, fabrication, assembly and CAD bonding. In that, they have proposed a soft clamp CAD model design that can catch or catch delicate objects like eggs, fruits, etc.
Example experiment and results.
Manufactured soft clamp is powered by gas pressure. It can contain elements like mouse, duster, egg, ball etc.
Some dimensions and design models are found on the basis of limitations and various challenges, the best designs are designed to form a soft clamp that are able to catch delicate objects like eggs, fruits. The soft gripper is made using 3D printers. Clamp silicone is made using rubber material. In experimental analysis and in the FEA-produced model. When errors and problems are corrected, the soft griper is adopted in the IRB 1410 robot, which is capable of catching soft materials such as egg, fruit and place.
Example 2. Soft pneumatic grippers embedded with stretchable electro-adhesion
Current soft condensing grippers cannot tightly capture flat materials and flexible objects without crushing on the curved surface. On the other hand, the current electro-adhesive tweezers are difficult to actively distort complex shapes to select surface or free-form objects. The PneuEA clamp is proposed to be implemented smoothly by the integration of an electro-adhesive clamp and soft two-finger ventilation gripper.
Electro-adhesive clamp soft carrier created it by splitting silicon sheet into two electro-designed designs and embedded in a soft electrolyte elastomer. The soft two-finger aerated clamp was created using the standard method of soft lithography. This innovative integration has linked the advantages of both electro-adhesive and soft air humid clamps. As a result, the proposed PUA clamp cannot choose flat, flat material like only porous fabrics and can take delicate items like light bulbs. Through the combination of two soft-touch sensors with a current, an intelligent and adaptive shape handling system for PneuEA content has been developed. In this example the work is expected to expand applications of soft grip and electro-adhesion technology.
The work presented in this example provides an innovative, efficient and easy light to implement PneuEA clip by integrating the electro-adhesive clamp on pneumatic impeller soft two cables on value development. Connecting the benefits of the proposed clamp electrochemical and soft pneumatic clamp. Not only the limitation of soft clamps to raise thin and flattened materials in this mix, but also the limitation of electron clamps to lift things from non-flat surfaces. As a result, the PUEA clamp is capable of controlling not only flat and flexible material but also complex shape materials. This can mean the ability of the current soft and electro-pneumatic grippers and can promote the application of electro-physic techniques and soft grippers. In addition, while absorbing electro-adhesion, the numerical clamp mechanical driving force can be reduced and more delicate substances can be controlled.
The main contributions of this document include:
(1) Combined electro-adhesion and soft pneumatic clamps, both enhance the efficiency of the technology
(2) Soft-touch include a custom sensor to ensure the PneuEA clamp is controllable and intelligent, and
(3) cost effective in the production of elastic electrodes Development of Approach Future Work Optimistic Design Clamp PneuEA and Performance and Intelligent PneuEA integration include 6DOF robot gripper for industrial materials pick and venue applications.
Example 3. Soft flexible gripper design, characterization and application
In this example, delicate objects represent the design concept of a soft floss accelerated gripper for manipulation. Traditional holders are composed of rigid components and have numerous passive joints. The more joints they are better, they can adapt to a specific object. However, connecting with delicate materials still requires specific control and some measurements.
In this paper, the authors present a proposal of a soft floss absorbent gripper, which is able to adapt to any additional computational EFF ORT or manipulated object shape without any sensor. Grinder only creates the same flue accessories as rubber and silicon. Because the gripper lacks any different connection and is acting through its simple deformity, it can take very complex shapes and thus easily conforms to the surface of the covered material.
This method is based on the soft pneumatic activators developed by the authors and its purpose can be easily redesigned to expand its application for special purposes. This paper introduces the design and practical qualifications of grip prototypes. Potential programs are discussed.
Traditional grippers are very widely used devices. However in some cases, the use of hard tools due to their STI FF is problematic. Soft and fall-free graspers and grippers perform more potential in such cases. Their abilities and soft contact makes them secure and is slim for delicate object manipulation.
Due to their security features, soft-grippers and graspers are considered as an alternative to rigid devices in human-current environments. Additionally, passive adaptation skills have made it possible for unstructured object manipulation in a specific environment and without using soft controls and FF OT without the use of soft devices. In many cases, there is no need to use any sensitivity to understand the work, as Gripper's eligibility returns to all the object irregularities.
Differences between IRB 120, UR5 and Sawyer
The ABB IRB 120 is the smallest robot available on ABB line 120. With only 25 kg, he manages to overcome larger rivals and provide objects that cannot be found anywhere else. It can be placed anywhere, even on top of other machines. ABB IRB 120 is portable and easy to integrate.
The new and used ABB IRB 120 IRC5 is useful in industries such as electronics, food and beverages, solar energy, pharmaceuticals, medicine and research. The compact Este six-axis robot can withstand loads of up to 3 kg. IRB 120 can be installed at any angle and is ideal for storing IRC 5 in narrow places. Cables are laid inside the lever to eliminate interference and provide flexibility for integration.
The lightweight aluminum casing, combined with powerful compact motors, gives this robot the opportunity to move with speed and precision. The IRB 120 uses an IRCCompact power controller for high accuracy and speed in a small package. This compact controller offers many advantages and allows you to program offline
Ur5 is a very flexible robot arm that allows you to safely automate repeated and hazardous functions. It helps your employee's time to increase the value of other parts of your production process. It can withstand a load capacity of up to 5 kg, which is 850mm long, and is the perfect solution for light support processes like collection, storage and testing.
In addition, UR5 is very easy to configure and programmed and provides the fastest peak in the industry. Establishment time, determined by the customer, is less than half a day and unpacking and installation can be done by a low employee in a short time. Programming with 3D visualization is also super-intuitive; Employees transfer robots only in the desired way, and then use a user-friendly tablet with a touch screen.
Sawyer is a revolutionary collaboration robot designed to do unrealistic automation tasks with traditional industrial robots. Sawyer offers a powerful automation with the Rethink brand, while maintaining synonyms for flexibility, security and power, which requires manufacturers.
Sawyer offered the freedom of a robot hand reaching 1260 mm, 7 degrees, which works hard-to-reach places in the workspace designed for people. Thanks to the built-in electrical accreditation tasks, he can take adaptive decisions to do the job so that the sire can work fine (+/- 0.1 mm) and work safely with the people
And I choose ABB IRB 120 because it offers a full range of robots to help manufacturers improve productivity, product quality, and worker safety. This is 4th generation robot technology is new to ABB. This material is ideal for loading and unloading and integrating, and provides an attractive, portable and lightweight solution for better control and accuracy.
Compact and lightweight
IRB For small design of 120, you can install anywhere in any corner – for example inside a cell, on top of a machine or close to other robots.
The IRB 120 is the most portable and lightweight in the 25 kg weight market. The cables are placed in the ears indoors to make clean and easy handling of clean surfaces, detect wind turbines, regulate the wrist from around the wrist and ensure smooth coordination.
Multipurpose
The IRB 120 is ideal for a wide range of industries, including electronics, food and beverages, engineering, solar energy, pharmaceuticals, medicine and research.
The food industry lubricant option (NSF H1) includes an ISO Class 5 clean room that provides safety and hygiene for food and beverages.
Optimized working range
The IRB 120 has a horizontal reach of 580 mm, which is the best move in its class, the ability to reach 112 mm below its base and a very compact turn.
Fast, accurate and agile
Designed with a lightweight aluminum structure, the engines ensure that the robot is capable of rapid acceleration and can also provide accuracy and maneuverability in any application. Using the IRB 120T option, the cycle time can be reduced to 25%, where the workpiece requires extensive reconstruction and mainly 4, 5 and 6 axes are used. This fast version is well suited for loading and packaging, as well as for controlled operations with PickPoster 3 ™.
IRC5 Compact controller – optimized for small robots
The new compact ABC compact IRB 5 controller displays the capabilities of the IRC5 controller in a compact format. It brings focus and speed control of applications that are unique to large installations and allow single-phase input, external connector for all signals and easy operation in 16, 16. Out. For offline programming, RobotStudio allows manufacturers to emulate the production cell for optimal robot positioning and provides offline programming to prevent costs over time and production delays.
Different sizes of bun

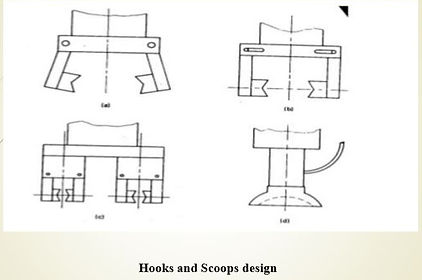









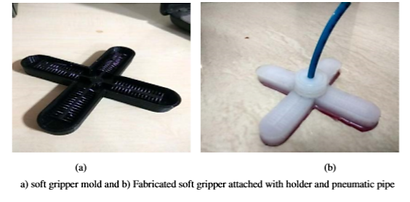





